HOME IMPROVEMENT
The Ultimate Guide to Self-Tapping Screws for Aluminum
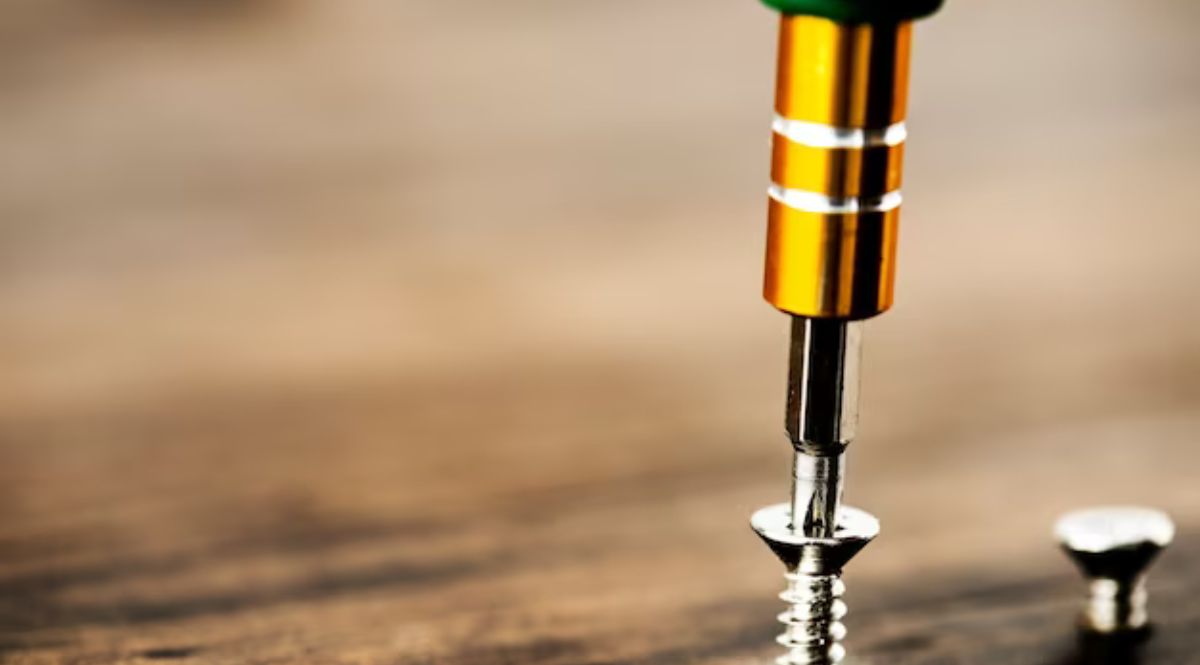
Aluminum is a lightweight metal that has several applications, including the aerospace and construction sectors. A self-tapping screw is an often-overlooked yet critical component when working with aluminum. In this detailed tutorial, we’ll learn all there is to know about self-tapping screws for aluminum, including what they are, how they may be used, and what benefits they offer.
Understanding Self-Tapping Screws
What Are Self-Tapping Screws?
The special thread on self-tapping screws allows them to start threading as they are pushed into the material. Self-tapping screws may be used to fasten many materials, including aluminum, without first needing pilot holes to be bored. Their capacity to drill their own holes increases their usefulness in many contexts.
How Do They Work?
Self-tapping screws have a pointed tip with threads that are designed to cut into their own material. These threads cut into the material when the screw is rotated, forming complementary threads. This method saves time and energy during assembly by obviating the requirement for tapping or pre-drilling holes.
Types of Self-Tapping Screws
Thread Forming vs. Thread Cutting
There are two main varieties of self-tapping screws, forming threads and cutting threads. Unlike thread-cutting screws, which use material removal to make threads, thread-forming screws actually displace the material as they work. Thread-forming screws are frequently used with aluminum because they provide stronger connections without degrading the material.
Materials and Coatings
Stainless steel, carbon steel, and even aluminum may all be used to make self-tapping screws. In addition, they may be coated with materials like zinc or nickel to increase their resistance to corrosion and longevity, particularly when used in hostile locations.
Benefits of Using Self-Tapping Screws
Efficiency in Aluminum Applications
The self-drilling feature of self-tapping screws makes them ideal for use with aluminum. Because of the time and money they save because of their efficiency, they are often used in fields where aluminum is present.
Reduced Pre-Drilling
To prevent stripping the material or snapping the screw, pre-drilled holes are necessary when using conventional screws. This is unnecessary with self-tapping screws, which streamlines the assembly process and lessens room for error.
Strong and Durable Connections
Self-tapping screws provide threads that are robust and long-lasting, so your aluminum parts will stay where you put them. In settings where security and stability are of the utmost importance, this dependability is indispensable.
Choosing the Right Self-Tapping Screw
Size and Length
A reliable joint can only be achieved by using self-tapping screws of the appropriate size and length. Over-tightening can weaken the aluminum, so be sure the screw is long enough to penetrate the substance.
Thread Type
Choose a thread variety that works for your project specifications. Check with the manufacturer to see which thread design they recommend for your specific use case.
Head Style
Self-tapping screws are available with a wide variety of head shapes. Head styles are selected based on personal taste and installation options.
Installation Tips
Preparing the Aluminum Surface
Make sure the metal is spotless before you begin putting the self-tapping screws. The screws will fit more securely and snugly if you do this.
Proper Torque and Speed
When working with aluminum, it is important to utilize the correct torque and speed settings on your power tool to avoid damaging the material and to achieve a secure connection. Excessive tightening might cause thread damage or even material failure.
Avoiding Over-Tightening
It’s important to tighten the screws enough to keep everything in place, but too much force might crack the aluminum or strip the threads. If accuracy is required, a torque wrench should be used.
Common Applications
Automotive Industry
Self-tapping screws are often used in the automobile sector for building aluminum elements including body panels and engine components. Because of their durability and effectiveness, they are frequently used by the automotive industry.
DIY Projects
Self-tapping screws are a common tool for do-it-yourselfers, who use them for anything from constructing aluminum frames to mending outdoor gear. They are a must-have for every do-it-yourselfer because of how convenient and dependable they are.
Electronics and Appliances
Self-tapping screws are commonly used by electronics and appliance manufacturers to fasten aluminum housings and parts. The gadgets’ durability and usefulness are guaranteed by these screws.
Advancements in Self-Tapping Screw Technology
High-Performance Coatings
High-performance coatings for self-tapping screws have been developed recently. Coatings like this make connections in aluminum structures last even longer by protecting them from corrosion and wear.
Innovative Thread Designs
Self-tapping screws have benefited from the continual development of new thread designs by engineers. In order to provide a more secure fit and enhanced load bearing capabilities, modern threads are designed to work with certain materials.
Environmental Impact
Aluminum’s Sustainability
Aluminum is eco-friendly because it can be recycled indefinitely without degrading. When used in conjunction with self-tapping screws, it aids in creating less wasteful buildings and products.
Recycling Self-Tapping Screws
Reusing or recycling self-tapping screws is another option for minimizing waste. These screws may be recycled at many scrap metal centers, saving space in landfills.
Maintenance and Care
Preventing Corrosion
Corrosion of self-tapping screws and aluminum components may be avoided with routine maintenance and inspections. Their service life can be lengthened in extreme conditions by using anti-corrosion treatments.
Regular Inspections
Aluminum is required to be inspected on an ongoing schedule to ensure there is no damage or wear. Any screws that self-tapping which demonstrate signs of corrosion or damage ought to be changed promptly.
Conclusion
Aluminum screws that self-tapping are a must possess for a wide variety of professional and do-it-yourself purposes. They are a wonderful choice for submitting because of their durability, straightforwardness, and the fact that threads may be manufactured without the need for a pilot hole to be present. The dimensions, thread type, and head design of the self-tapping screws you purchase will determine how powerful and permanent your connection will be. Self-tapping screws are a vital component to guaranteeing the durability of your aluminum construction sites, provided they are attached and maintained properly.
Frequently Asked Questions (FAQ’s)
- How do self-tapping screws differ from regular screws?
- There is no need for pilot holes when using self-tapping screws since their special thread design allows them to form threads as they are driven in. The hole for standard screws must be drilled ahead of time.
- Can I use self-tapping screws on other materials besides aluminum?
- Self-tapping screws are often utilized with aluminum, although other materials like wood and plastic can be fastened with the right screw for the job.
- What is the maximum thickness of aluminum for self-tapping screws?
- Self-tapping screws, depending on criteria such as screw size and type, may often pierce metal up to a certain thickness. It is crucial to use the product in accordance with the manufacturer’s instructions.
- Do I need special tools to install self-tapping screws?
- Self-tapping screws may be installed with either common power equipment or by hand. It is essential, however, to utilize the correct torque settings and guarantee accurate alignment.
- Can self-tapping screws be removed and reused?
- As long as they are not damaged, self-tapping screws may be taken out and used again. When extracting the screw, be careful not to bend or strip the threads.
HOME IMPROVEMENT
Fitout Interiors: Transforming Spaces with Style
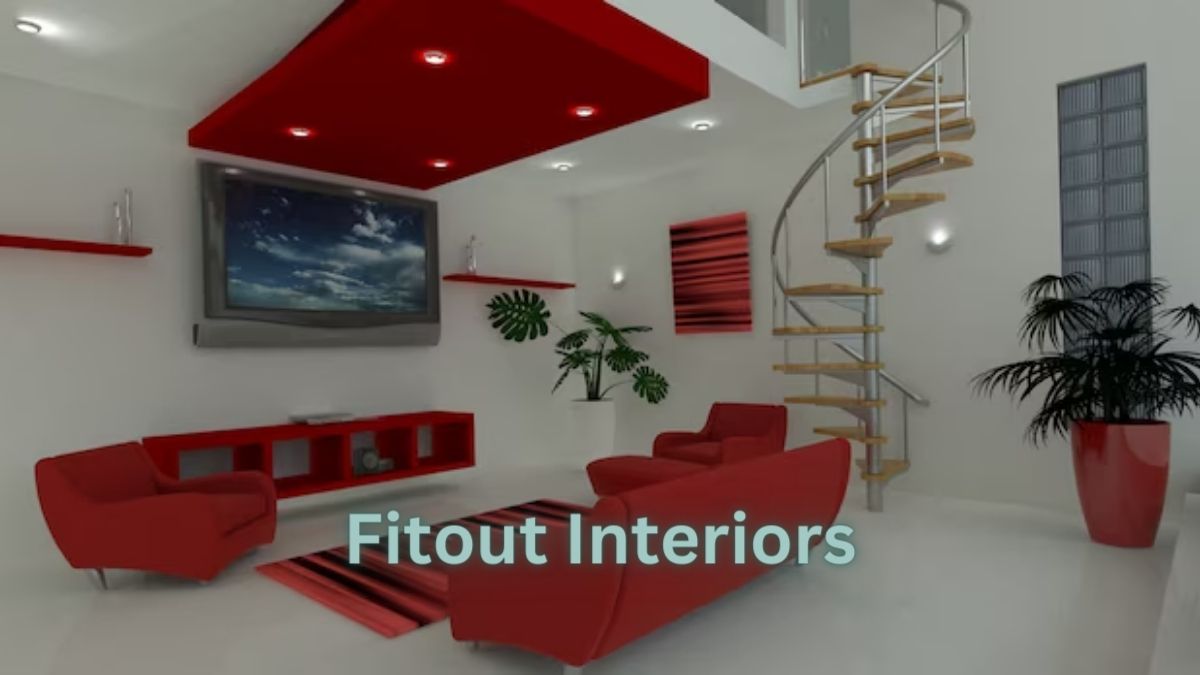
Fitout interiors have become increasingly significant in today’s society, where first impressions are crucial. Interior fit-outs improve the usability and attractiveness of a building’s interior by redesigning and decorating existing rooms. The interior design and decoration of your house or workplace may have a major effect on the mood of the place. This article looks into the topic of fitout interiors, including its meaning, importance, many varieties, and best practices.
1.What Is a Fitout Interior?
The act of designing and outfitting a building’s interior is known as a fitout. Interior design is the art and science of enhancing a room to better serve its intended function via strategic placement of furnishings and accessories. Everything from the paint to the furniture to the accessories are part of the fitout interiors.
2.The Importance of Fitout Interiors
A well-executed fitout interior is crucial since it may change a boring room into a practical, attractive, and cosy one. The interior of a building plays an essential function in people’s lives, whether it’s the place of employment where workers spend an important part of their day or a house wherever they make memories alongside the people they love.
3.Factors to Consider in Fitout Interiors
- Budget: The first stage of every interior fit out project is to establish a budget. It helps with prioritizing design components and making sure you don’t go overboard with costs.
- Space Utilization: Maximizing the space’s usefulness is an important part of b. Space use. It’s important to maximize usable space when designing interior fitouts.
- Aesthetics:The significant role of aesthetics cannot be underestimated. The design of the room should convey the personalities of the people who will be using the location and make them feel welcome.
4.Types of Fitout Interiors
- Commercial Fitouts: Commercial fitouts are establishment-specific renovations. Their goal is to design places that encourage work, interaction with customers, and company identity.
- Residential Fitouts: Homes are designed with the occupants’ comfort, practical needs, and individual sense of style in mind in b. residential fitouts.
5.The Role of an Interior Designer
Designers of interior fitouts are called interior architects or designers. They use their knowledge of aesthetics, space planning, and design concepts to make a home more beautiful inside and out.
6.Benefits of Professional Fitout Interiors
Expert interior fitout designers take a holistic view. They alleviate tension and work to ensure your goals are met.
7.DIY vs. Professional Fitouts
While do-it-yourself renovations might save money, they often take more time and effort and provide less professional results. Expertise is worth the extra expense for professional fitouts.
8.Choosing the Right Fit Out Interior Company
Choosing a reliable interior fitout firm is essential. Examine their previous work, check out some evaluations, and think about how they approach design to make an informed choice.
9.Trends in Fitout Interiors
The latest styles in home decor are always changing. If you keep up with the newest trends, you may furnish and decorate your home in a way that is both modern and chic.
10.Sustainability in Fitout Interiors
Concern for the environment is on the rise. Fitout interiors that make use of eco-friendly products and practices assist lessen their influence on the environment.
11.The Process of Fitout Interior Design
Consultation, planning, design, building, and final touches are all part of the interior design process.
12.Common Mistakes to Avoid
It can be expensive and time-consuming to fix mistakes made during interior fitouts. If you know what hazards to look out for, you can avoid them.
13.Conclusion
Fitout interiors are about more than simply making a place seem nice; they should also promote health and productivity without sacrificing aesthetics. Whether you’re redecorating your home or your place of business, fitout interiors may make a world of difference.
14.FAQs
1.How much does a professional fitout interior cost?
The price tag on a professional fitout might rise or fall based on factors like the size of the space being renovated and the quality of the business chosen.
2.What are some popular interior design trends for 2023?
Sustainable architecture, minimalist aesthetics, and biophilic architecture are all on the rise.
3.Can I mix DIY and professional fitout approaches?
DIY and professional design may work together to save money.
4.How long does it take to complete a fitout interior project? The typical time frame for a project is a few weeks to a few months.
5.Do I need to hire an interior designer for a small project?
DIY approaches or enlisting professional design advice are both viable options for smaller projects.
HOME IMPROVEMENT
No Drill Cabinet Lock for Hinged Glass Door: Keeping Your Valuables Safe
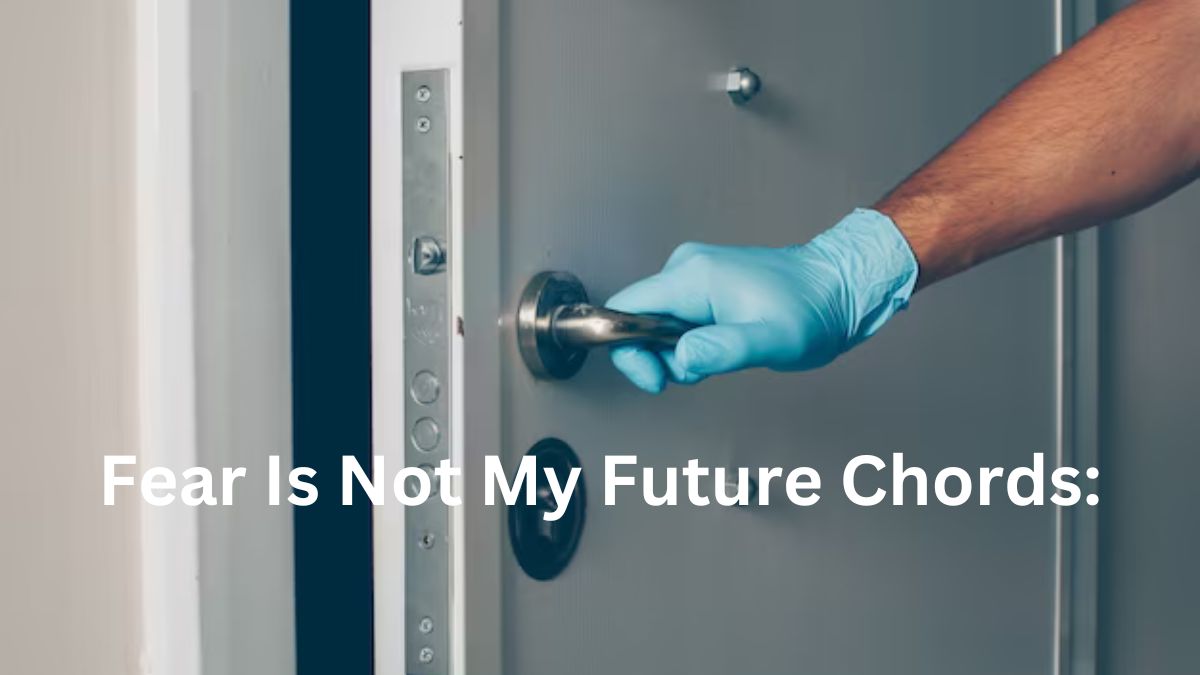
Protecting yourself, your family, and your possessions in today’s dangerous environment is a top priority. The proper locking system is crucial for cabinets with hinged glass doors. This article delves into the topic of No Drill Cabinet Lock for Hinged Glass Door covering such topics as its utility, advantages, and installation.
The Importance of Cabinet Locks for Hinged Glass Doors
Hinged glass door cabinets are a modern and chic option for showcasing your valuables. However, they frequently lack protection, leaving them open to intrusion. Locks on cabinets serve an important purpose in this context. They add an added level of security, warding off inquisitive dogs, youngsters, and attackers alike.
Types of Cabinet Locks for Hinged Glass Doors
It’s necessary to be familiar with the many styles of no-drill cabinet locks before delving into their technicalities. Magnetic locks, sticky locks, and latch mechanisms are all examples. Different varieties are available, each with its own set of advantages and qualities.
Benefits of No-Drill Cabinet Locks
Because of its convenience and security, no-drill cabinet locks are becoming increasingly used. Among the many benefits are:
- No Damage: These locks don’t need to be drilled into your cabinets, so your furniture will be safe from harm.
- Ease of Installation: Putting it in place is a breeze because you won’t require any specialized equipment or training.
- Removability: When they are no longer required, these locks may be removed without leaving any traces.
- Versatility: No-drill locks are convenient since they may be used on many different types of cabinetry.
How to Choose the Right No-Drill Cabinet Lock
The best no-drill cabinet lock for you will rely on aesthetic tastes, level of security needed, and the type of cabinet you have. Think about the substance of the cabinet and the lock before making any purchases. Making a good choice requires lots of study.
Installation of No-Drill Cabinet Locks
The setup procedure is easy to follow. The different parts of the lock have to be attached to the cabinets, the surface needs to be cleaned, and the lock must have the opportunity to be set as recommended by the manufacturer. You are able to secure your cabinet in only a couple of seconds.
Child Safety and No-Drill Cabinet Locks
Grandparents placed a premium on the well-being of their kids’ security. If you want to keep your kids from getting into your cabinet of medicines or cleaning products, a no-drill cabinet lock is an excellent choice. They provide you assurance that your child’s inherent curiosity won’t get them into danger.
Pet Safety and No-Drill Cabinet Locks
Pets may be just as inquisitive as kids sometimes. The no-drill locks on your cabinets will not only keep your belongings safe, but they will also prohibit your dogs from getting into anything dangerous. When dealing with poisonous materials or delicate items, this is crucial.
Top Brands and Products
We’ve rounded up the industry’s finest names so you can pick wisely. Reviews have been quite favorable due to the products’ dependability and user-friendliness. Brands like Safety 1st, Dreambaby, and BabyKeeps are among the market leaders.
Maintenance and Care
Maintaining your cabinet lock routinely is crucial to extending its life. Remove any dirt or debris from the lock and its parts. If required, apply grease to the moving components. This will keep the lock operating smoothly and efficiently.
Common Issues and Troubleshooting
No-drill cabinet locks are a product, thus they can break down like any other. To help you keep your cabinets in tip-top shape, this section addresses frequent issues and offers advice for fixing them.
Customer Reviews and Recommendations
Feedback from those who have actually used these locks in the past is invaluable. To help you make an informed decision, we have compiled evaluations and suggestions from actual users of no-drill cabinet locks.
Advantages of No-Drill Cabinet Locks
The benefits of no-drill cabinet locks are outlined in this section, with an emphasis on how well they work to secure cabinets with hinged glass doors.
Disadvantages of No-Drill Cabinet Locks
There are certainly a number of benefits to using no-drill cabinet locks, but it’s additionally essential to be aware of possible disadvantages, such as lock failure or difficulties opening.
Conclusion
In conclusion, if you’re looking to increase safeguarding without sacrificing the look of your cupboards, a No Drill Cabinet Lock for Hinged Glass Door is an excellent choice. These locks are advantageous because of how simple they are to install and how numerous distinct kinds of doors and windows they can protect.
Frequently Asked Questions (FAQs)
Are no-drill cabinet locks suitable for all types of cabinets?
It’s important to make sure that your particular cabinet design is compatible with no-drill cabinet locks before purchasing.
Can I remove a no-drill cabinet lock without damaging the cabinet?
To answer your question, no-drill cabinet locks are made specifically to be removed without harming the finish of the cabinet.
Are these locks easy to install for someone with no DIY experience?
The setup procedure is straightforward and does not call for any specialized knowledge or equipment.
Do no-drill cabinet locks work on glass cabinets with wooden frames?
These locks are adaptable; you may use them with a wide range of glass cabinets and frames.
What are some alternatives to no-drill cabinet locks for hinged glass doors?
Adhesive locks, magnetic locks, and latch systems are among alternatives; each has its own benefits and drawbacks.
HOME IMPROVEMENT
Contractors Choice Painting and Home Improvement: Transforming Your Space
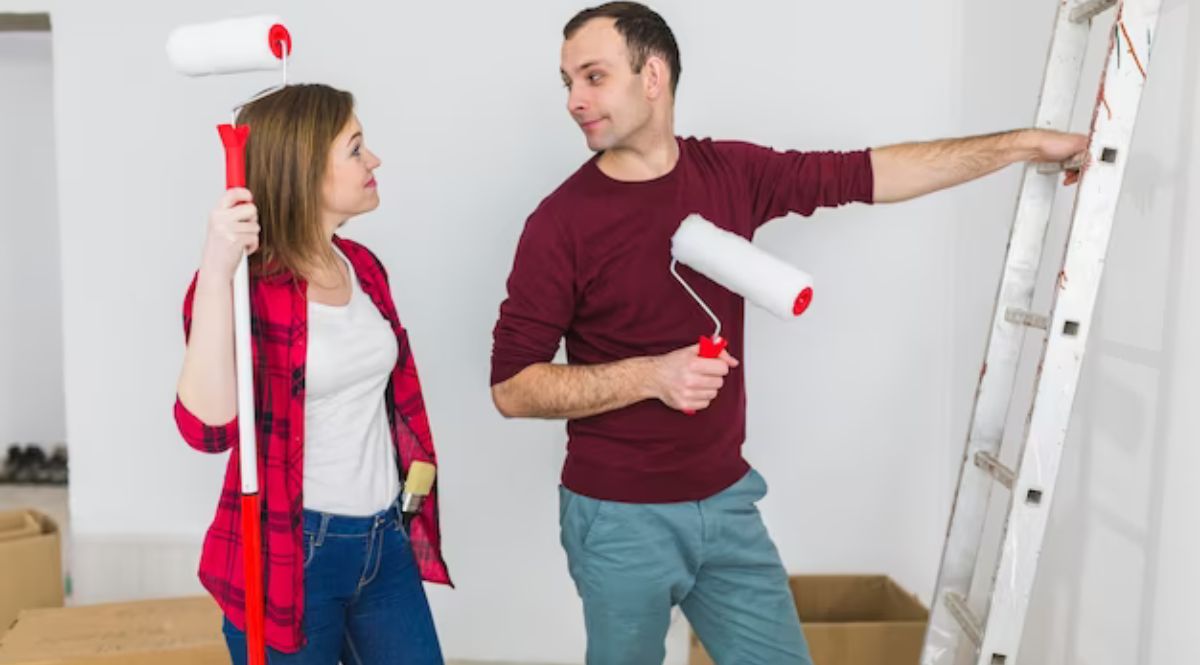
Choosing the best contractor to work on your house may make a world of difference. This article explores Contractors Choice Painting and Home Improvement and reveals what makes them successful. We’ll look at the many reasons why you should choose them to furnish and decorate your home, including their high quality of work and dedication to their customers.
A Legacy of Excellence
For nearly twenty years, people have trusted Contractors Choice Painting and Home Improvement. Since its founding in 2001, this family-run business has maintained a reputation for producing work of the highest quality. Their passion for their work shows in every drop of paint and hammer blow.
The Expert Team
Professionals with years of experience are the backbone of Contractors Choice. Painting is just one of several home renovation services that they are well-versed in providing. This group guarantees a flawless outcome to your project thanks to their attention to detail and dedication to accuracy.
Services Offered
If you need any kind of home renovation work done, Contractors Choice has you covered. You may count on them for everything from a new coat of paint to a complete overhaul.
- Painting Services: Contractors Choice Painting is the best choice if you want to update the inside or outside of your property. Their expert painters will utilize only the finest supplies and methods to bring your ideas to life.
- Home Renovations: Wish you had a more roomy bathroom or brand new kitchen? Renovations are the company’s bread and butter, therefore they’re named appropriately. They collaborate with you closely to actualize your vision and provide aesthetically pleasing and practically useful results.
- Exterior Upgrades: Enhancing your home’s façade may do wonders for its marketability. Contractors Choice can do everything from installing new siding to building a deck to improve your home’s curb appeal.
Unparalleled Customer Satisfaction
Painting and Home Improvement Contractors’ Top Priority is Satisfying Their Clients. They take into account that your house is an extension of your character and strive to meet or surpass your standards.
Tailored Solutions
Contractor’s Choice tailors their services to each individual client since they understand that every job is different. They take in what you have to say and offer advice based on their experience, so that the final product is exactly what you had in mind.
Quality Assurance
At Contractors Choice, we place a premium on quality. Each project is built to last using only high-quality materials and standard procedures. Your money will be well spent because of our dedication to excellence.
Testimonials
Listen to what actual clients have to say about Contractors Choice Painting and Home Improvement instead of simply taking our word for it:
- “Contractors Choice completely renovated my antiquated kitchen into a state-of-the-art work of art. I am overjoyed beyond words. – Sarah M.
- “They pay the closest attention to detail. My neighbors are still raving about the outside painting work they did for me. – John D.
- “Working with the crew at Contractors Choice was a breeze. Their skill and dedication to their work are unparalleled. By Emily R.
Conclusion
If you’re looking for a home renovation company, Contractors Choice Painting and Home renovation is the gold standard. They are the best option for remodeling your living spaces because of their long history of excellence, their knowledgeable staff, and their dedication to your pleasure.
FAQ’s
- Are they licensed and insured?
- Yes, Contractors Choice has all the necessary permits and insurance to provide you peace of mind while working on your project.
- What areas do they serve?
- They mainly work in [list service areas], however it’s best to double-check with them about particular places.
- Do they offer eco-friendly options for painting?
- If you’re concerned about your carbon impact, you’ll be happy to know that they sell environmentally friendly paint.
- How long does a typical home renovation project take?
- A project’s duration is proportional to its complexity. During the initial meeting, Contractors’ Choice will provide you an estimated completion date.
-
TECH8 months ago
Exploring the Exciting Features of PHP Version 8.1 for Enhanced Web Development
-
CRYPTO4 months ago
Unlocking the Potential: Understanding WalletConnect là gì
-
NEWS5 months ago
Bestadvise4u.com News: Your Gateway to Informed Living
-
ENTERTAINMENT5 months ago
“кинокрадко” – Unmasking the Culprit Behind Film Piracy
-
TECH4 months ago
“몽세리 266b+v”: Revolutionizing Technology for a Better Future
-
HEALTH5 months ago
Tough Tissue Muscle Connector: The Unsung Heroes of Movement
-
WINDOWS11 years ago
(solved)-Windows update cannot currently check for updates, because the service is not running. You may need to restart your computer
-
WINDOWS9 years ago
(Solved) – “How do you want to open this type of file (.js)?” Windows 8/8.1